Sewn type VS High-frequency hot-pressing type reflective piping
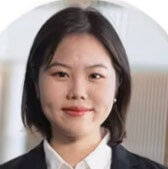
MAX Reflective Accessories Design Director
Reflective piping is crucial in manufacturing safety gear, outdoor apparel, and sportswear. These reflective features enhance visibility in low-light conditions, ensuring safety and aesthetic appeal. However, not all reflective piping is made the same.
Two primary manufacturing methods dominate the market: sewn type and high-frequency hot-pressing (HF heat-pressing) type reflective piping. Choosing between them depends on your product’s requirements, durability needs, and cost considerations.
In this blog, we explore the components, production steps, advantages, and disadvantages of these two types of reflective piping, helping you select the best option for your needs.
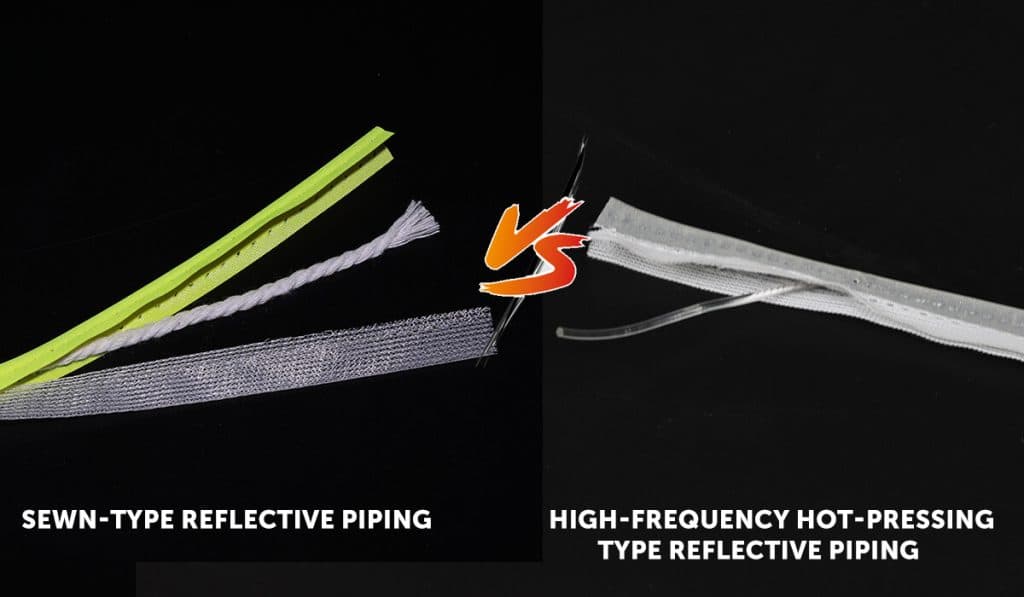
Components of reflective piping
Reflective piping combines various materials assembled to provide visibility, durability, and functionality.
Reflective Layer
The reflective layer consists of micro glass beads or prisms, embedded in reflective fabric or heat transfer fabric. These layers vary in performance, size, and finish, offering options like reflective polyester fabric, flame-retardant cotton fabric, stretch reflective fabric, or even premium TPU film. Popular widths for reflective piping are between 1.5 cm and 2.5 cm, whether stitched or heat-pressed.
Cotton core or PVC tubes
- Sewn types: Incorporate cotton cores of 2 mm–3 mm thickness, commonly white or grey.
- Heat-Press types: Use PVC tubing with a 0.2–0.3 cm diameter, often embedded for increased strength and elasticity.
Auxiliary Fabrics
Nylon or polyester mesh fabrics are integrated into sewn reflective piping. These auxiliary fabrics ensure easier stitching by widening the seams and providing flexibility.
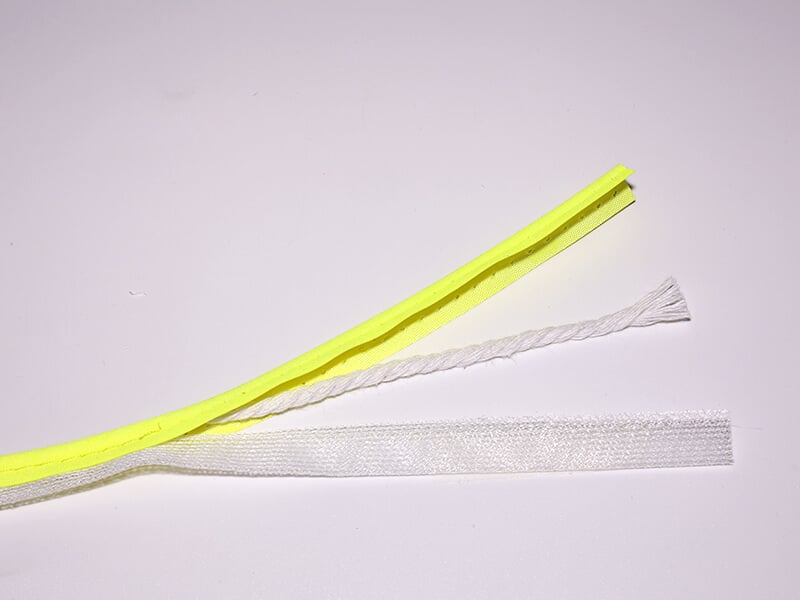
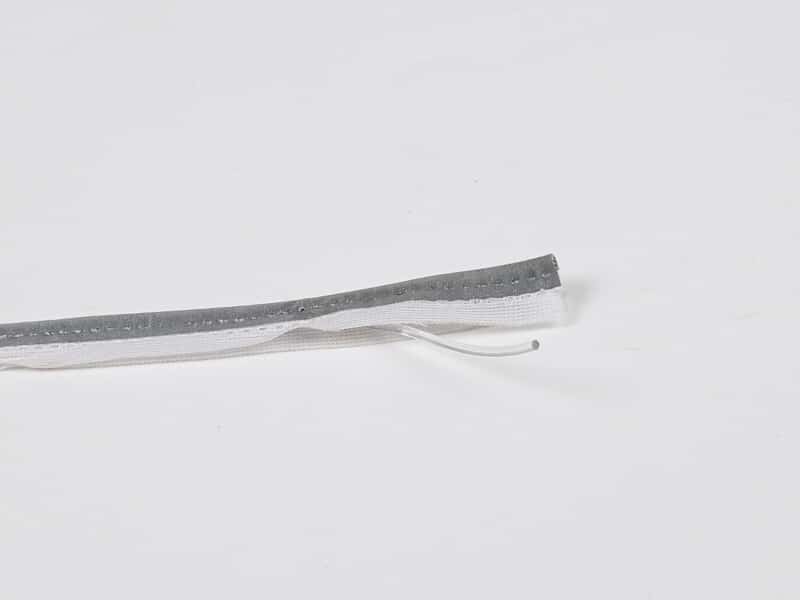
Sewn-type reflective piping
What is sewn-type reflective piping?
Sewn-type reflective piping is created by stitching the reflective materials onto the underlying fabric using industrial sewing techniques. This method allows for high precision and customization.
Steps to make sewn-type reflective piping
- Cutting: Reflective layers are cut into strips sized between 15–25 mm, while auxiliary fabrics like mesh are tailored to dimensions customized to client requirements.
- Finishing: The cotton core is folded in half and sewn into the reflective fabric using a standard or specialized edging sewing machine. The auxiliary mesh fabric is stitched simultaneously for enhanced ease during further sewing.
Advantages of sewn-type reflective piping
- Highly customizable for different designs and widths.
- Does not require a significant investment in equipment.
- Suitable for projects that require frequent adjustments or repairs.
Disadvantages of Sewn Type Reflective Piping
Stitching can wear out due to exposure to harsh environments like constant friction or water.
Discover more about MAX's reflective piping products.
High-frequency hot-pressing (HF Heat-Pressing) type reflective piping
What is HF Hot-Pressing Reflective Piping?
The HF heat-pressing method uses high-frequency heat to bond reflective fabric without stitching. This process ensures a seamless, waterproof finish ideal for durable reflective products.
Steps for HF heat-pressing reflective piping
- Hot pressing: HTV materials (heat transfer vinyl) are cured at high temperatures to bond the reflective layer securely. Premium versions may use 3M Scotchlite™ or reflective TPU film for superior wash resistance. Care is taken to protect materials from sparks during curing.
- Assembly: A PVC pipe is inserted into the reflective strip, which is then folded in half and sealed using precise high-frequency heat pressing for a streamlined finish.
Advantages of HF hot-pressing reflective piping
- Produces piping with superior water resistance and durability.
- Ideal for mass production, as it is faster and more efficient.
- Offers a seamless, clean aesthetic without exposed stitching.
Disadvantages of HF hot-pressing reflective piping
- Limited customization compared to sewn types.
- Requires specialized high-frequency machines, increasing initial setup costs.
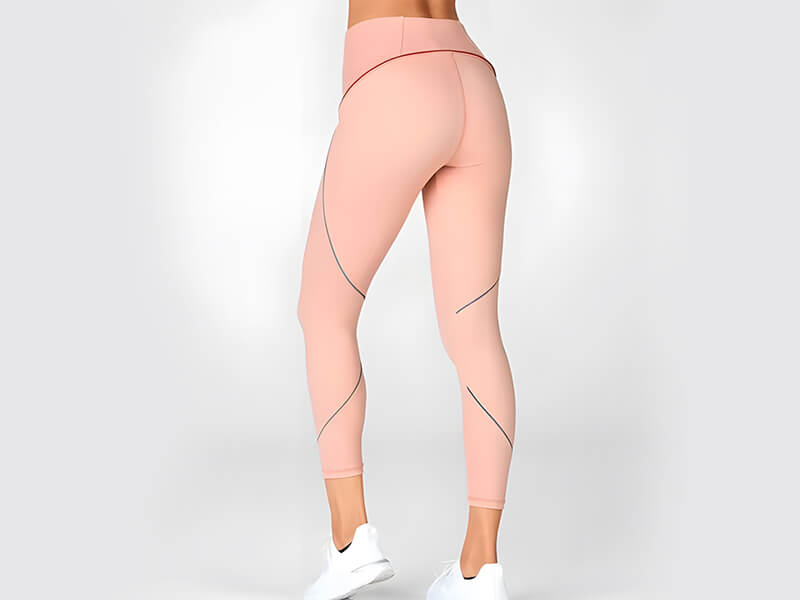
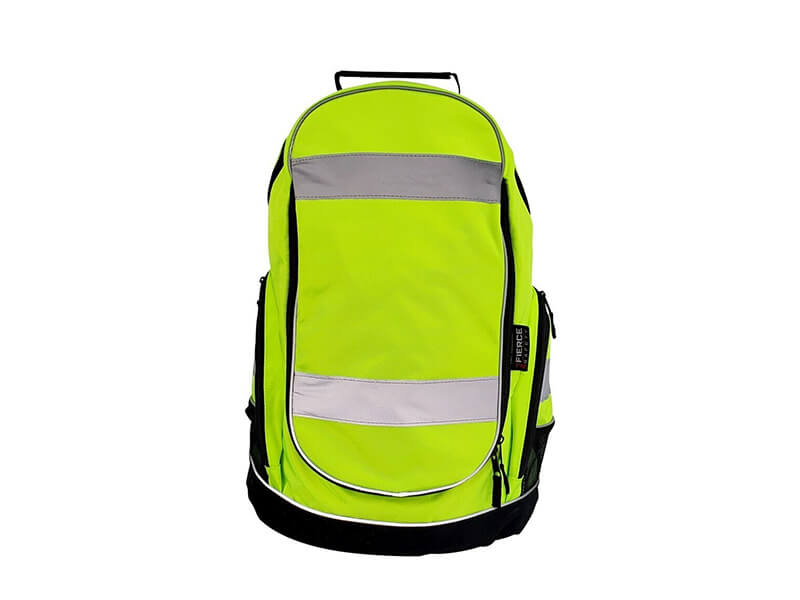
Sewn type VS High-frequency hot-pressing type reflective piping
Feature | Sewn Type | HF Hot-Pressing Type |
Production Method | Manual stitching | Automated heat pressing |
Customization | Highly customizable | Limited flexibility |
Durability | Good but stitching may degrade | Excellent water and wear resistance |
Cost | Lower initial investment | Higher initial equipment cost |
While sewn piping is the go-to choice for projects needing intricate designs, HF heat-pressing piping excels in high-volume manufacturing where durability and waterproof performance are critical.
Which type is right for you?
Choosing the correct type of reflective piping depends on your product’s application:
- Sewn Type:
Ideal for projects requiring manual customization and small-scale production.
Suitable for items with unique or intricate designs, where repairs may be necessary, such as artisanal outdoor or safety-wear brands.
- High-frequency hot-pressing type:
This type is ideal for mass production where waterproofing and durability are required. It works well in harsh environments or with rigid fabrics, such as construction equipment, premium sportswear, and luggage.
Conclusion
Reflective piping is an essential feature in many industries, but choosing between sewn type and HF heat-pressing type depends on factors like durability, customization needs, and scalability. Sewn reflective piping offers versatility, while HF heat-pressing ensures efficiency and resilience.
At MAX, we provide high-quality sewn and HF hot-pressing reflective piping solutions tailored to your unique needs. Contact us today for expert advice and premium products that meet your specifications.
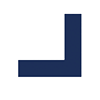
Related blogs
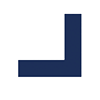