Common Reflective Piping Problems and How to Avoid Them
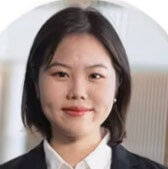
MAX Reflective Accessories Design Director
Reflective piping is crucial in many industries, from safety gear to activewear. Its ability to enhance visibility, especially in low-light conditions, makes it indispensable. However, like all materials, reflective piping is not without challenges.
In this blog, we’ll discuss some of the common issues encountered with reflective piping and provide actionable solutions to help you maintain the quality and performance of your products.
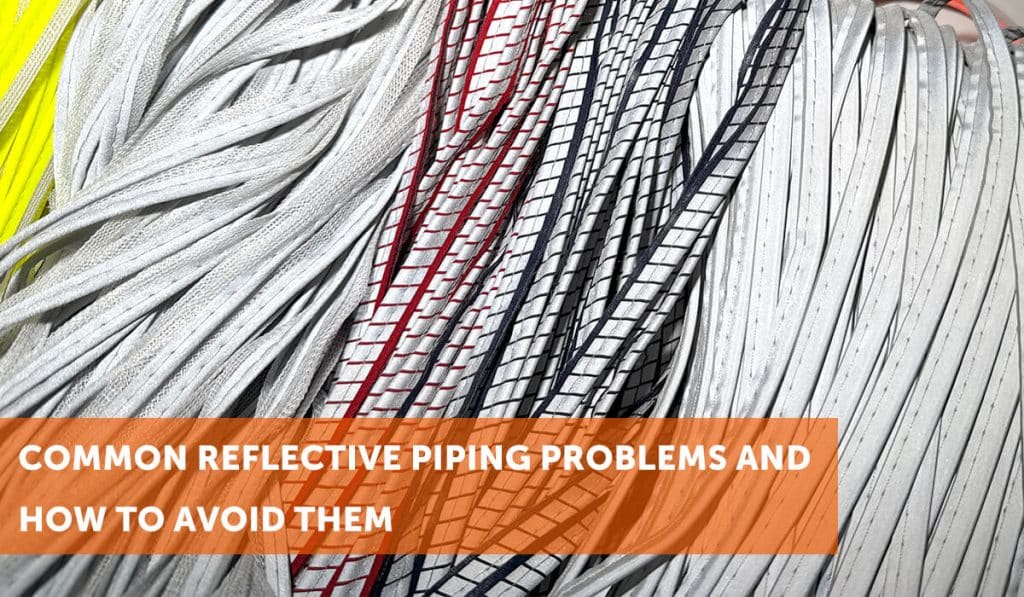
Sewing Weaknesses
Problem:
If reflective piping is not sewn securely, it may peel off or detach during wear or repeated washing, compromising the product’s functionality and aesthetics.
Solution:
To prevent this issue, it’s essential to use proper sewing techniques:
- Reinforce seams: Use serged seams or overlock stitches to strengthen the stitching. These methods ensure tighter and more durable attachments.
- Choose high-quality threads: Invest in durable, heavy-duty threads that withstand repeated wear and washing cycles.
- Test before production: Conduct rigorous sewing tests to verify that the reflective piping stays intact under stress.
By adopting these practices, you can minimize sewing-related problems and extend the lifespan of your reflective piping.
Reflective Coating Damage
Problem:
Reflective piping owes visibility to tiny glass beads or other reflective coatings embedded in the material. However, these coatings are susceptible to damage, particularly during industrial cleaning processes like power washing. Over time, aggressive washing can cause the beads to loosen and leave the piping dull.
Solution:
Careful handling and cleaning techniques are essential to preserving the reflective quality:
- Gentle Washing: Opt for hand washing or gentle machine washing cycles rather than high-pressure or rough industrial washes.
- Avoid Harsh Chemicals: Strong detergents and bleach can erode the reflective coating, so stick to mild cleaning agents.
- Air Dry Instead of Heat Dry: Tumble drying can damage the reflective surface, so hang the product to air dry instead.
- Customizable solutions: If your reflective piping will face unique cleaning or industrial usage conditions, communicate these needs to your supplier to customize the product accordingly.
By adopting these cleaning practices, you can safeguard the integrity of the reflective coating and ensure it operates efficiently for an extended period.
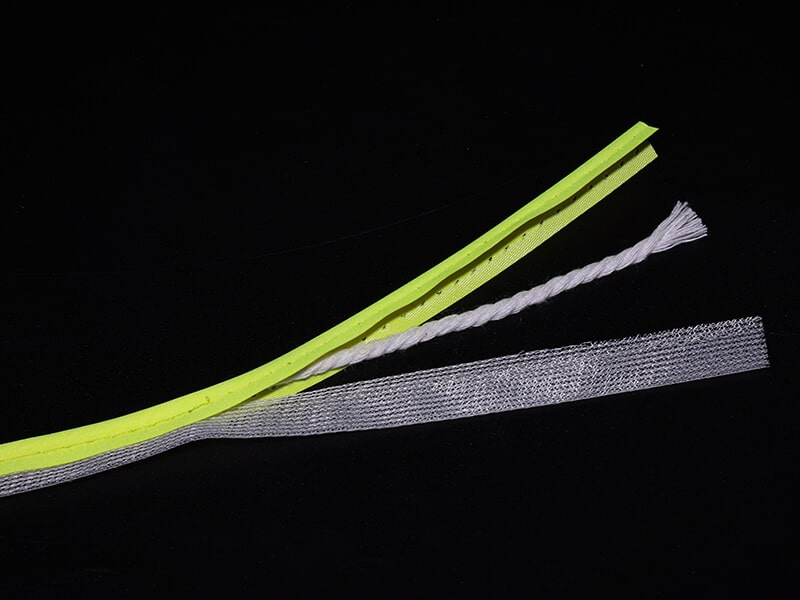
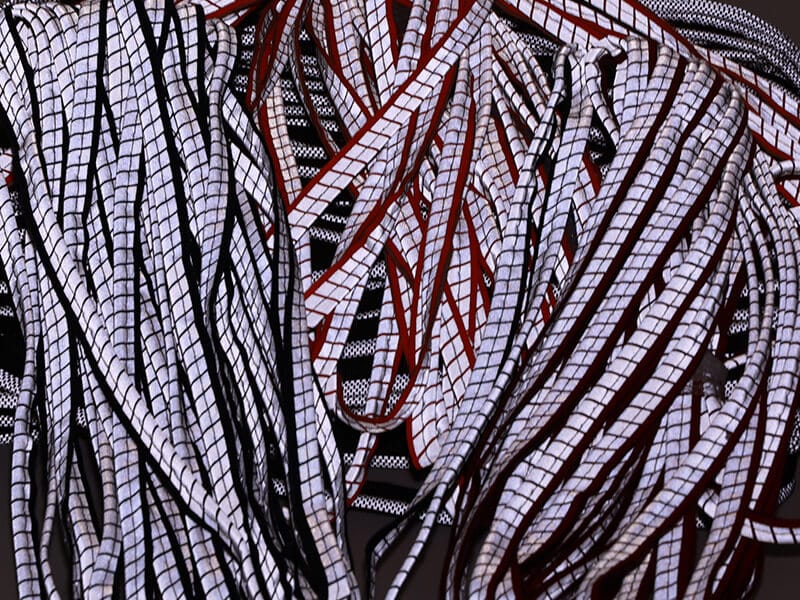
Adhesion Failure in Hot Application Pipes
Problem:
The adhesive used to attach reflective piping can weaken in hot environments or during high-temperature applications, leading to detachment or reduced effectiveness.
Solution:
Avoid adhesion failures by following these steps:
- Adhere to Temperature Guidelines: Always follow the manufacturer’s recommended temperature settings during application and processing.
- Request Guidance: If your product is to be used in high-heat environments, consult your supplier for recommendations on heat-resistant adhesives.
- Trial Runs: Before large-scale production, test samples in relevant conditions to ensure the adhesive performs reliably.
Your reflective piping can withstand demanding application conditions by proactively managing temperature-related challenges without compromising adhesion.
General Tips for Long-Lasting Reflective Piping
In addition to addressing specific problems, here are some general strategies to enhance the durability and usability of reflective piping:
- Inspect Before Use: Conduct quality checks to ensure all reflective piping meets specifications before sewing or application.
- Store Properly: Reflective materials should be stored in cool, dry environments, away from direct sunlight or excessive humidity to prevent deterioration.
- Communicate Application Needs: Clearly outline the intended use of the piping with your supplier, as custom solutions may be available based on your requirements.
- Stay Updated: Stay informed with industry advancements and innovations in reflective materials. Technology continually evolves, providing better solutions for durability and performance.
Composition and Manufacturing Process of Reflective Piping
Closing Thoughts
Reflective piping plays a vital role in many industries, and while it offers exceptional benefits, it’s essential to address its common issues during production and use proactively. Whether it’s sewing weaknesses, coating damage, or adhesion failures, following best practices can ensure your reflective piping performs effectively and lasts longer.
If you need further assistance or are considering volume production with specific requirements, please get in touch with our team.MAX is happy to work with you and customise a solution that meets your needs. Let’s work together to make your products shine day or night!
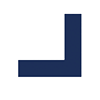
Related blogs
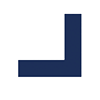