ANSI Hi-Vis Standard
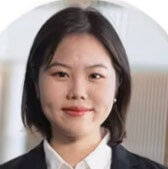
MAX Reflective Accessories Design Director
In high-risk environments, visibility can be a matter of life or death. Whether workers are operating machinery, working on busy roads, or performing tasks in low-light conditions, their visibility is critical in preventing accidents.
The ANSI (American National Standards Institute) Hi-Vis Standard provides guidelines for the design and performance of high-visibility apparel, ensuring workers are easily seen in environments with low visibility, such as construction sites or roadways.
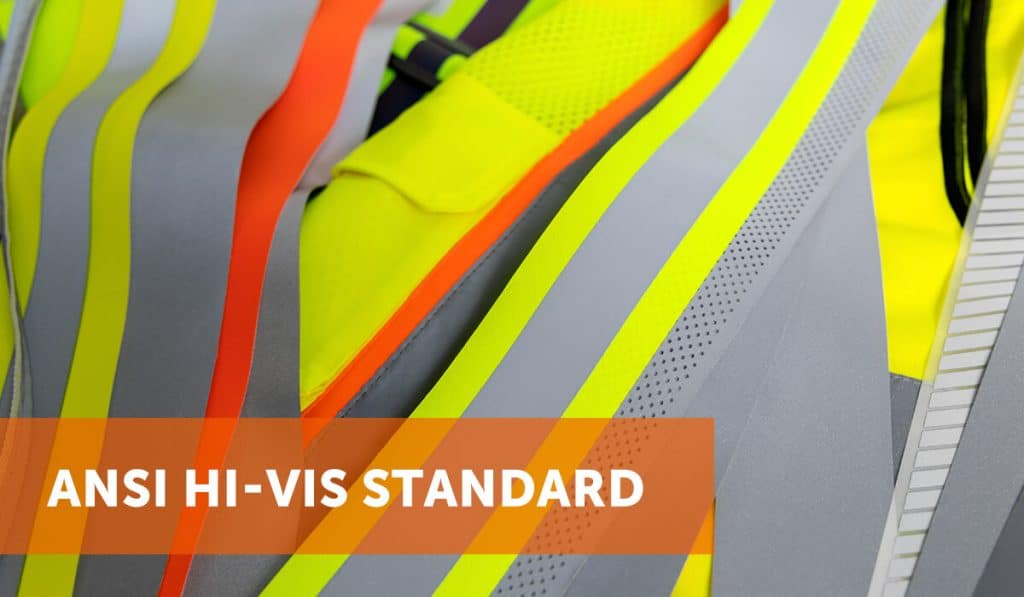
What is ANSI?
The ANSI Hi-Vis Standard sets guidelines for high-visibility clothing designed to make workers more visible in dangerous work environments. This standard helps prevent accidents, especially near moving vehicles, heavy equipment, or dangerous machinery.
Developed by the American National Standards Institute (ANSI) and the International Safety Equipment Association (ISEA), these standards focus on the design and performance of reflective clothing. They apply to workplaces like construction sites, roadwork, and factories. The standards are updated regularly to stay in line with new safety needs and technology.
ANSI is a nonprofit that creates safety standards to ensure products and services are safe and reliable. This helps protect people, health, and the environment.
The ANSI/ISEA 107 standard is specifically for high-visibility safety wear. It explains what materials, colors, and reflective features the clothing should have to make workers visible and reduce the risk of accidents. Manufacturers widely follow this standard to ensure safety in various.
Understanding ANSI/ISEA 107 Standard
The ANSI Hi-Vis Standard classifies high-visibility clothing into different categories based on the work environment and level of risk. This helps ensure that workers are seen and safe, especially in areas with traffic or other hazards. Here’s an overview:
Classes of High-Visibility Clothing:
Class 1: Low Visibility Areas:
- Designed for workers in environments with minimal traffic and low risk. These garments offer basic visibility.
- Typical Users: Parking lot attendants, warehouse workers.
- Minimum Requirements: At least 155 square inches of reflective material and 2 square inches of fluorescent fabric.
Class 2 – Moderate Visibility Areas:
- For workers exposed to moderate traffic or conditions with low lighting, like roads with vehicles moving at 35 mph.
- Typical Users: Construction workers, utility workers, roadside workers.
- Minimum Requirements: At least 201 square inches of reflective material and 3 square inches of fluorescent fabric.
Class 3 – High-Visibility Areas:
- For environments with high traffic or low visibility, these garments provide the highest level of visibility.
- Typical Users: Emergency responders, construction workers on highways, or workers in fog or rain.
- Minimum Requirements: 310 square inches of reflective material and 4 square inches of fluorescent fabric.
Types of Hi-Vis Garments:
- Type O (Off-Road): For areas without traffic, providing basic visibility, like construction sites or rural areas.
- Type R (Roadway): For workers near traffic, providing higher visibility, typically used in road construction zones.
- Type P (Public Safety): For first responders and emergency workers, offering the highest visibility to ensure they are seen in all conditions, day or night.
- Supplemental Class E: Class E garments provide extra visibility, like reflective pants or bibs, and are worn with Class 2 or Class 3 gear for added safety.
The ANSI/ISEA 107 Standard ensures that workers are visible in various environments, providing clear guidelines on visibility requirements for different levels of risk.
Design and Materials for High-Visibility Clothing: Key Requirements of ANSI/ISEA 107 Standard
High-visibility clothing is designed to ensure the safety of workers in both daylight and low-light conditions. These garments combine various materials and follow specific design guidelines to maximize visibility. The ANSI/ISEA 107 standard outlines the key requirements for these garments, including material types, reflective elements, and design specifications.
1. Materials for high-visibility clothing
High-visibility clothing is made from a combination of fluorescent and reflective materials, ensuring visibility in different lighting conditions:
- Fluorescent Background Material: These brightly colored fabrics, such as fluorescent yellow, orange, or red, are designed for daytime visibility. They increase the wearer’s presence during the day, even from a distance.
- Reflective Materials: Reflective strips or bands are critical for nighttime visibility. They reflect light, such as from vehicle headlights, back to the source, helping the wearer stand out in low-light environments.
The combination of these materials ensures visibility both during the day and at night, helping to protect workers in all weather conditions.
2. Key Requirements of the ANSI/ISEA 107 Standard
The ANSI/ISEA 107 standard ensures that high-visibility apparel meets specific performance criteria to protect workers in various environments.
- Material and Reflectivity Requirements: The standard mandates the use of fluorescent materials for daytime visibility and reflective materials for nighttime or low-light visibility. The reflective tape must be durable and capable of withstanding repeated washing while maintaining its retroreflective properties.
- Reflective Tape Placement: The standard specifies that reflective tape should be placed in specific patterns to maximize visibility. For example, horizontal bands of tape should be placed around the torso, and vertical bands should cover the shoulders. The tape must be at least 2 inches wide and should be placed so that it is visible from all angles, ensuring full visibility of the wearer.
- Design and Durability Expectations: ANSI/ISEA 107-compliant garments are designed to withstand harsh work environments. They should offer comfort and functionality, ensuring that the high-visibility materials do not hinder the wearer’s movement. Garments must also retain their durability and performance after repeated washing, with reflective elements tested for colorfastness and retroreflective performance.
- Coverage Area and Minimum Visible Material Requirements: The standard outlines the minimum area of the garment that must be covered in high-visibility material. For example, Class 3 garments require at least 775 square inches of fluorescent material and 201 square inches of reflective material. The reflective tape must be strategically placed to enhance visibility from all angles, such as around the waist, chest, arms, and legs.
- Color Combinations, Contrast Requirements, and Pattern Guidelines: To maximize visibility, ANSI/ISEA 107 specifies that fluorescent materials must be in bright, easily noticeable colors such as fluorescent yellow-green, orange-red, or red. The reflective tape should contrast well with the background material, typically being silver or white. The reflective tape should be arranged in a pattern, such as two vertical stripes on the front and back of a vest and a horizontal stripe around the waist, creating an obvious outline that is recognizable to oncoming traffic or equipment.
Application and Usage
The ANSI Hi-Vis standards are crucial in ensuring worker safety across a wide range of industries. High-visibility apparel is essential for protecting workers in environments where they may be exposed to moving vehicles, heavy machinery, or other potential hazards.
The ANSI/ISEA 107 standard provides clear guidelines for using high-visibility clothing to maximize visibility and reduce the risk of accidents. Below, we discuss how these standards apply to various industries and consider environmental factors that impact visibility.
Construction Industry
In the construction industry, workers often operate in areas with heavy machinery and fast-moving vehicles. Construction zones can be chaotic, with workers and vehicles constantly in motion.
ANSI Hi-Vis standards are crucial in ensuring that workers, especially those working near traffic or operating heavy machinery, are visible to others.
Construction workers typically wear Class 2 or Class 3 garments, depending on the level of risk. For example, a worker on a busy highway construction site would wear a Class 3 garment to ensure they are visible from a distance, while a worker on an indoor construction site with minimal traffic might only need a Class 1 garment.
Day and night visibility are both important considerations in the construction industry. During the day, fluorescent yellow-green or orange garments stand out against construction materials and equipment. At night or in low-light conditions, reflective tape provides essential visibility, especially when illuminated by headlights or worksite lighting.
Transportation Industry
In the transportation industry, particularly for road workers, railroads, and airport ground crews, high-visibility apparel is a critical safety feature. These workers are frequently near moving vehicles, such as cars, trucks, trains, or aircraft, which pose a significant risk.
ANSI/ISEA 107 standards are applied rigorously, and workers typically wear Type R (Roadway) or Type P (Public Safety) garments. The Class 3 level of protection is often required for workers who are exposed to high-speed traffic or on busy highways.
Environmental factors play a significant role in the transportation industry. Daytime visibility is essential to avoid accidents, but night visibility is just as important. Workers on highways or railways need garments that not only stand out in daylight but also reflect light in low-light conditions. Weather conditions, such as rain or fog, can also reduce visibility, making it essential for workers to wear durable, weather-resistant high-visibility gear that remains effective in such conditions.
Emergency Services
For emergency responders, such as firefighters, police officers, and paramedics, high-visibility apparel is essential for both daytime and nighttime operations. In emergencies, clear visibility is crucial for ensuring safety and preventing accidents.
Emergency services personnel typically wear Type P (Public Safety) garments, which are designed to provide maximum visibility in high-risk environments. These garments often incorporate reflective tape and bright fluorescent materials to ensure they can be seen from a distance, even in crowded or chaotic situations.
Emergency responders are frequently exposed to both day and night conditions, so their high-visibility apparel must be effective at all times.
Additionally, these workers often operate in hazardous environments such as accident scenes, where weather conditions like rain, snow, or fog may further reduce visibility. ANSI-compliant gear helps ensure they remain visible despite the challenges posed by their environment.
General Industry
In general industry settings, high-visibility apparel is worn by workers in manufacturing plants, warehouses, logistics, and other environments where heavy machinery or vehicles are used.
The level of visibility required depends on the specific risks in the workplace. In lower-risk areas with minimal vehicle movement, workers may wear Class 1 garments. In areas where workers are exposed to moving vehicles or heavy equipment, Class 2 or Class 3 garments may be required.
In the general industry, visibility needs vary with the type of work being done. For instance, workers inside factories may need to wear high-visibility clothing to be seen by others operating large machinery.
On the other hand, warehouse workers or those in outdoor settings must be visible not only during the day but also in low-light conditions such as early mornings or evenings. These garments also need to account for various weather conditions, such as rain or snow, which can reduce visibility.
Environmental Considerations
- Day vs. Night Visibility: High-visibility gear must be designed for use both during the day and at night. Fluorescent colors are effective during the day, as they stand out in bright sunlight, while reflective materials are crucial for nighttime or low-light conditions, when workers are exposed to moving vehicles or equipment.
- Weather Conditions: Weather conditions like fog, rain, or snow can reduce visibility, making it even more important for high-visibility apparel to remain effective in all weather conditions. ANSI/ISEA 107 compliant garments are often designed with weather-resistant materials to ensure durability and performance, even in challenging conditions.
- Work Environment Factors: The nature of the work environment significantly influences the level of visibility required. For example, workers in construction zones or on busy highways will need garments that offer high visibility from all angles, often requiring Class 3 protection. In contrast, workers in less hazardous environments may only need Class 1 or Class 2 garments. Factors such as traffic speed, the presence of machinery, and environmental factors like lighting or weather play key roles in determining which level of ANSI Hi-Vis garment is appropriate.
Compliance and Certification
Ensuring that high-visibility apparel meets ANSI/ISEA 107 standards is crucial for worker safety. Manufacturers must undergo a thorough certification process to guarantee that their garments are compliant. This section explains the compliance process, including initial certification, ongoing compliance, laboratory testing procedures, and labeling requirements, to ensure products meet safety standards.
Initial Certification
The first step in achieving ANSI/ISEA 107 compliance is the initial certification of the high-visibility apparel.
Manufacturers must submit their garments to accredited testing laboratories to assess whether the materials, design, and performance meet the specifications outlined in the ANSI/ISEA 107 standard. The testing process evaluates various factors such as the visibility of the fluorescent materials in daylight, the effectiveness of the reflective tape in low-light conditions, and the durability of the materials under normal working conditions.
Once the garments pass the required tests, they receive certification, which allows the manufacturer to label the product as ANSI/ISEA 107 compliant. This certification process ensures that the apparel meets all the requirements for visibility, safety, and performance, providing confidence that the garments are suitable for use in hazardous work environments.
Ongoing Compliance
Ongoing compliance is an essential part of maintaining ANSI/ISEA 107 certification. Manufacturers must regularly review and update their products to ensure they continue to meet the safety standards, especially when there are updates to the ANSI/ISEA 107 standard itself. This includes retesting garments for performance, especially after design or material changes.
Additionally, manufacturers are responsible for ensuring that their production processes consistently result in garments that meet the same standards as the initial certified samples. This may involve conducting internal quality control checks and working with accredited laboratories for periodic re-testing.
Ongoing compliance also includes monitoring the performance of the reflective materials and fluorescent fabrics after washing and regular wear to ensure they maintain their visibility and durability. Products that do not meet the standards after a period of use or after changes in production may lose their certification, so manufacturers must ensure that all their garments consistently perform as expected.
Laboratory Testing Procedures
Laboratory testing is a critical step in the compliance process. Accredited testing laboratories are responsible for conducting various tests to determine whether high-visibility garments meet the requirements set forth by the ANSI/ISEA 107 standard. Key tests include:
- Visibility Test: The garment’s fluorescent material is tested for its ability to reflect daylight and be visible in bright conditions. The fabric must meet specific color and brightness standards to qualify for certification.
- Retroreflective Performance Test: Reflective materials are tested to ensure they can reflect light effectively in low-light conditions. The reflective tape is measured for its retroreflectivity, which determines how well it will shine back when exposed to headlights or other light sources.
- Durability Test: The garment’s durability is assessed, particularly how well it withstands washing, wear, and exposure to harsh working conditions. The reflective materials and fluorescent fabrics must maintain their visibility even after several washes and prolonged exposure to environmental factors.
These tests are essential to confirm that the high-visibility apparel meets the ANSI/ISEA 107 standards and is suitable for use in hazardous environments.
Labeling Requirements
To ensure that high-visibility garments meet ANSI/ISEA 107 standards, they must be clearly labeled with essential information. Proper labeling helps users identify the product’s compliance and provides important details about the garment’s performance, care, and intended use. The key labeling requirements include:
- Compliance Marking: The label must display a statement indicating that the garment complies with the ANSI/ISEA 107 standard. This statement may include the exact version of the standard the garment complies with, such as ANSI/ISEA 107-2015.
- Class and Type Information: The label must specify the class (1, 2, or 3) and type (O, R, or P) of the garment. This provides essential information about the garment’s intended use and the level of visibility it offers. For example, a Class 3 Type R garment is designed for high-risk environments near roadways.
- Manufacturer Information: The label should include the manufacturer’s name, brand, or identification number to allow traceability in case of recalls or quality concerns.
Care Instructions: To maintain the garment’s reflective and fluorescent properties, the label must include proper care instructions. These instructions typically outline recommended washing methods, temperature guidelines, and whether the garment is machine washable or requires special handling. This ensures that the garment maintains its visibility after repeated use. - Size Information: The garment must include clear size labeling, ensuring that the wearer selects the correct fit for maximum visibility and comfort.
- Reflective Tape Placement and Design: In some cases, the label may also include information on the placement of reflective tape, ensuring the wearer understands the garment’s reflective coverage and how it contributes to overall visibility.
Conclusion
Hi-Vis apparel is crucial to maintaining workplace safety, especially in hazardous environments such as those involving moving vehicles, heavy machinery, or poor lighting. The ANSI/ISEA 107 standard plays a vital role in ensuring worker visibility and reducing the risk of accidents in hazardous environments. By adhering to ANSI ratings, materials, and garment types, employers can select the right Hi-Vis garments for their employees, ensuring compliance with safety regulations and promoting a safer work environment.
At MAX, as a leading Hi-Vis manufacturer, we emphasise the importance of choosing the right equipment for a particular work environment. Make safety a priority by choosing ANSI/ISEA 107-compliant apparel to ensure your employees remain visible and protected.
Don’t wait – equip your team with the best Hi-Vis gear today and uphold the standards that protect them.
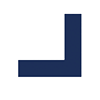
Related blogs
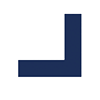
Related products
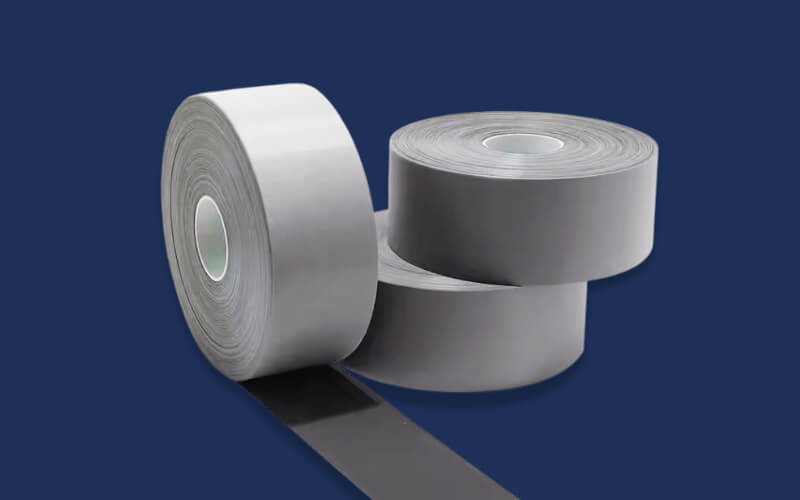
Reflective Tape For Clothing
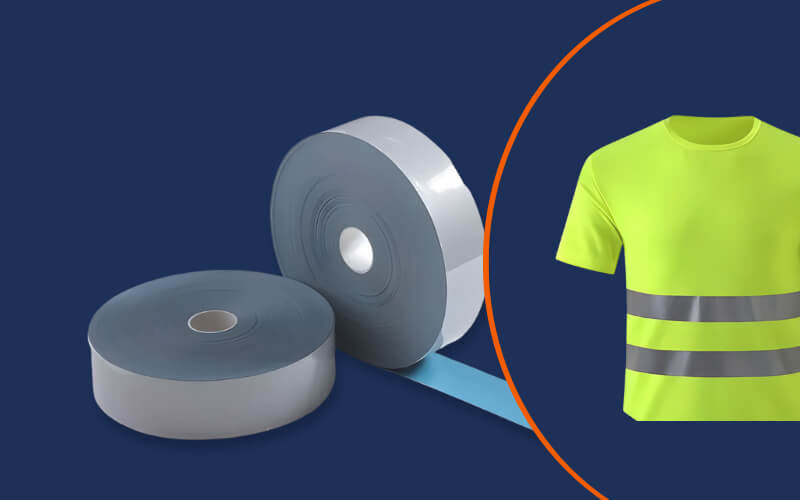
Reflective Heat Transfer Vinyl
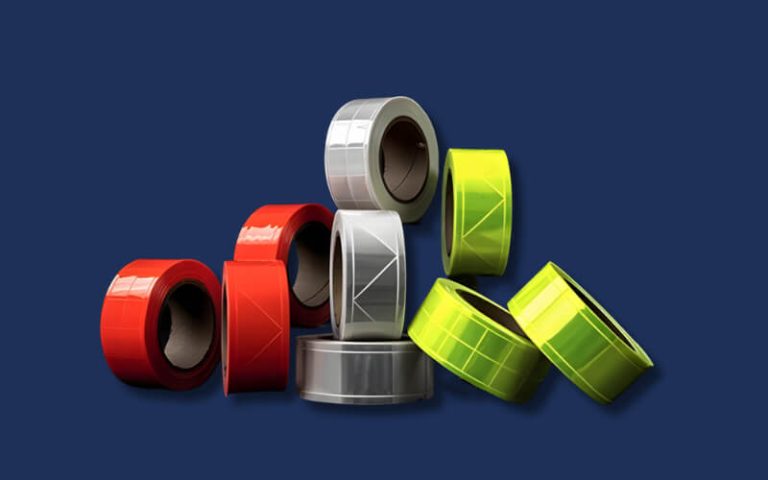
PVC Reflective Tape
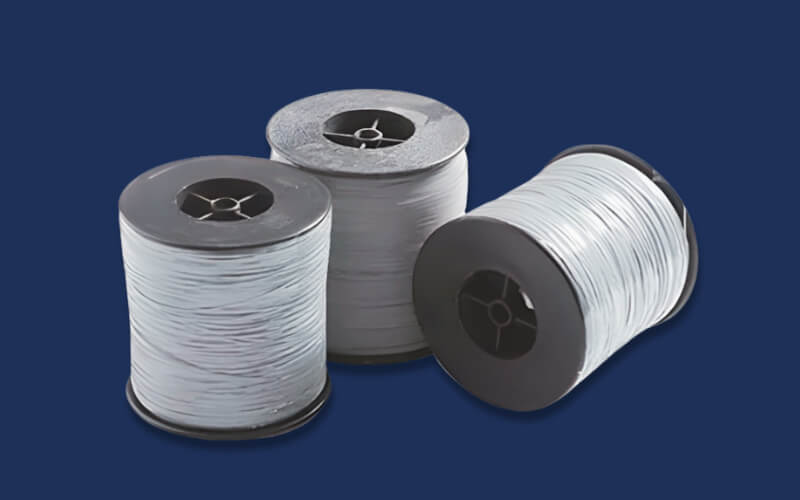